HP 315 latex 54" printer.
I’m having banding issues with my HP 315 It started happening on a few recent prints, I ran cleanings, alignment, test plots, nozzle tests, and color calibrations. All seemed normal. I printed solid CMYK squares and they printed with very little banding. So I swapped all my heads for new ones. Upon taking out the old I discovered ink sludge on a 2 of them. The rest were also not looking so good, The ports they sit in had sludge in them too and on the electrical pads. Attached are pics. I cleaned them best I could, but now the banding is worse. I am running cleanings now but at a loss as to what to do.
My maintenance cartridge is at 15%. The old heads were from 2/2020 Attached are pictures of what I am describing
I’m having banding issues with my HP 315 It started happening on a few recent prints, I ran cleanings, alignment, test plots, nozzle tests, and color calibrations. All seemed normal. I printed solid CMYK squares and they printed with very little banding. So I swapped all my heads for new ones. Upon taking out the old I discovered ink sludge on a 2 of them. The rest were also not looking so good, The ports they sit in had sludge in them too and on the electrical pads. Attached are pics. I cleaned them best I could, but now the banding is worse. I am running cleanings now but at a loss as to what to do.
My maintenance cartridge is at 15%. The old heads were from 2/2020 Attached are pictures of what I am describing
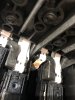
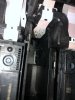