jimmyheartcore
New Member
Hey guys, I was advised in the Newbies forum to repost this here.
I am in need of some advice on our current situation. Be warned, it is a long and boring story, but we're kind of at the end of our rope and need some advice.
I have been working at my current job for a little over a month. My employers purchased a brand new Mutoh ValueJet 1614 last August, and have been experiencing a lot of problems. Most notably, a vertical banding issue that is prevalent and consistent. The ironic thing is that the 1614 has a "Wave Pattern Technology" that is supposed to eliminate banding. The dealer has led us through many possibilities in regards to the issue, including using crappy material, improper settings, and incorrect ICC profiles. None of these issues have fixed the problem. It is part of my job here to figure all of this out and get this printer properly running.
Come to find out, when the printer was delivered 10 months ago all of the shock sensors were broken. The driver signed off on this, and it was reported to the dealer immediately. The sale associate instructed us to accept the shipment, and said he was noting it in our file.
Over several months we reported various issues with the printer to the dealer, the most predominant being the vertical banding issue. When I began here, I had never seen an issue like the banding they were experiencing. It was very sporadic but consistent at the same time. It wasn't lining up to the rollers, nor the fan/vacuums. I became very proactive about fixing the issue when I started here.
We have had techs come out several times to fix the printer, but the problem is never fixed. Though different things will make the print improved, they just seem to act as a band-aid on the issue.
This is my employers' first printer and after reporting the shock sensors they set up the printer and it appeared to be doing fine. After printing for a couple weeks they realized that the vertical banding was happening, and put in a support ticket for it. The dealer led them around all of the different issues (material, settings, etc.) and my employers thought it was something they were doing wrong, not the printer, because the dealer led them to believe that.
The dealer recently sent a tech out to service the machine (who works directly for the dealer, not Mutoh), after which we decided that adjusting the head height and slant improved the print considerably, but the bands were still visible. He assured us that with the information about the damaged shipment, and his reputation and service history at Mutoh, he would be able to get us a working replacement sent out. He apologized for the issue not being fixed sooner, and told us how the sales person who sold us the machine was fired months ago for not properly performing his job.
The tech returned back to the dealer, and his boss wrote us a letter stating that they are "not prepared to take any additional actions and this matter will be considered resolved". However, the issue isn't resolved, and the printer is still under warranty -- it is still printing those awful vertical bands.
We are running out of time on the 1-year warranty, and short on ideas.
My employers are very upset with our dealer currently, and it seems like whenever I try and get help directly from Mutoh they either plainly ignore me or forward me to the dealer (who isn't helping much).
What do you guys think we should try?
Here are a couple of photos of the banding:
The banding issue is less apparent in some colors. We have lost customers, and have comped orders due to the printer's output. Some of the prints come out okay, like I said -- it all depends on the colors. But even in the prints that are "okay" the banding is still there. A customer might not notice it, because they don't know to look for it. But I see it, and that is bad enough.
Thank you in advance for your insight.
I am in need of some advice on our current situation. Be warned, it is a long and boring story, but we're kind of at the end of our rope and need some advice.
I have been working at my current job for a little over a month. My employers purchased a brand new Mutoh ValueJet 1614 last August, and have been experiencing a lot of problems. Most notably, a vertical banding issue that is prevalent and consistent. The ironic thing is that the 1614 has a "Wave Pattern Technology" that is supposed to eliminate banding. The dealer has led us through many possibilities in regards to the issue, including using crappy material, improper settings, and incorrect ICC profiles. None of these issues have fixed the problem. It is part of my job here to figure all of this out and get this printer properly running.
Come to find out, when the printer was delivered 10 months ago all of the shock sensors were broken. The driver signed off on this, and it was reported to the dealer immediately. The sale associate instructed us to accept the shipment, and said he was noting it in our file.
Over several months we reported various issues with the printer to the dealer, the most predominant being the vertical banding issue. When I began here, I had never seen an issue like the banding they were experiencing. It was very sporadic but consistent at the same time. It wasn't lining up to the rollers, nor the fan/vacuums. I became very proactive about fixing the issue when I started here.
We have had techs come out several times to fix the printer, but the problem is never fixed. Though different things will make the print improved, they just seem to act as a band-aid on the issue.
This is my employers' first printer and after reporting the shock sensors they set up the printer and it appeared to be doing fine. After printing for a couple weeks they realized that the vertical banding was happening, and put in a support ticket for it. The dealer led them around all of the different issues (material, settings, etc.) and my employers thought it was something they were doing wrong, not the printer, because the dealer led them to believe that.
The dealer recently sent a tech out to service the machine (who works directly for the dealer, not Mutoh), after which we decided that adjusting the head height and slant improved the print considerably, but the bands were still visible. He assured us that with the information about the damaged shipment, and his reputation and service history at Mutoh, he would be able to get us a working replacement sent out. He apologized for the issue not being fixed sooner, and told us how the sales person who sold us the machine was fired months ago for not properly performing his job.
The tech returned back to the dealer, and his boss wrote us a letter stating that they are "not prepared to take any additional actions and this matter will be considered resolved". However, the issue isn't resolved, and the printer is still under warranty -- it is still printing those awful vertical bands.
We are running out of time on the 1-year warranty, and short on ideas.
My employers are very upset with our dealer currently, and it seems like whenever I try and get help directly from Mutoh they either plainly ignore me or forward me to the dealer (who isn't helping much).
What do you guys think we should try?
Here are a couple of photos of the banding:

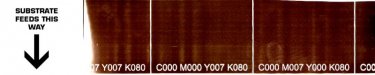
The banding issue is less apparent in some colors. We have lost customers, and have comped orders due to the printer's output. Some of the prints come out okay, like I said -- it all depends on the colors. But even in the prints that are "okay" the banding is still there. A customer might not notice it, because they don't know to look for it. But I see it, and that is bad enough.
Thank you in advance for your insight.
Last edited by a moderator: